POWDER INJECTION MOLDING TECHNOLOGY FOR
LARGE METAL & CERAMIC COMPONENTS & SYSTEMS
SME
TECHNICAL PAPER (note: figures removed)
Society of Manufacturing Engineers One SME Drive, Dearborn, MI 48121 313-271-1500 www.sme.org
Boney A. Mathew
Mathson Materials Technology, Inc. 1845 Thunderbird Street Troy, MI 48084, USA
ABSTRACT
Traditional applications for metal injection molding or
ceramic injection molding have been small net shaped
parts exhibiting design and economic benefit over
wrought or cast components. A new water based agar
binder system for metal and ceramic injection molding
has been developed that offers the ability to produce
large thick parts in range of 1 to 2 kg which are
competitive with those produced by investment casting.
Other significant advantages of this system are a clean
and rapid debind, and the ability to mold into soft
tooling. As a result, savings are achieved not only by
eliminating machining and other processing steps but
also by reduced development and inventory costs. This
technology is applied to a variety of automotive
applications such as, EGR System, Exhaust System, Oxygen
Sensors, Electrical Components, Engine Components, etc.
Many of these applications require demanding mechanical
properties. For an example, the average tensile
properties of the 17-4PH stainless steel alloy is
compared against wrought and cast properties, tensile
properties were essentially equivalent to wrought and
exceed typical cast properties. Due to the relative low
molding pressure and temperature required for water
based agar binder, soft tooling may be employed in place
of hardened tools for production runs less than 10,000
parts. Primary materials using water-based agar binding
systems are Stainless Steel, Alumina, Zirconia, Steatite
and other metal alloys. This injection molding process
allows economical competition with large net shaped
process techniques such as Investment Casting.
The importance of this paper is that it allows designers
and engineers to utilize Ceramics and Metal Alloys
Injection Molding Technology to combine several machined
or cast components into one large cost effective system
eliminating several manufacturing steps.
INTRODUCTION
The injection molding for metal and ceramic powders are
production technologies that are experiencing rapid
growth worldwide. This growth is mainly in the USA,
Europe and Asia. Ceramic Injection Molding (CIM) and
Metal Injection Molding (MIM) is a manufacturing
technique for making complex and precision components.
Ceramic and Metal Injection molded components compete in
the market place against parts made using various
processes. Investment Casting, Slip Casting, Machining
and Powder Forging are examples of the competitive
processes. An important part of CIM and MIM is the
binder in the feedstock technology and removal of binder
from the part after injection molding. One binder
technology currently established is the polyacetal-based
binder. The polyacetal based binder systems uses a
catalytic debinding utilizing Nitric Acid as
depolymerization Catalyst.1. New development in binder
technology such as aqueous based agar binder systems for
metal and ceramic offers the ability to produce large
thick parts in the range of 1 to 2 kg which are
competitive with those produced by Investment Casting.
THE AGAR BASED AQUEOUS BINDER SYSTEM
This binder is based on agar, a polysaccharide derived
from seaweed, which is water-soluble. Metal or ceramic
powder is mixed with the water, agar and a gel
strength-enhancing agent having the form of a borate
compound such as calcium borate, zinc borate, etc. to
form feedstock pellets that can be injection molded into
components2.
The use of such gel forming materials in combination
with a gel strength-enhancing additive substantially
reduces the amount of binder (typically 2-3 wt %) needed
to form a self-supporting article. Thus complex
components produced from agar with gel strength
enhancing borate compounds imparts high strength and
deformation resistance. It is critical to have adequate
part green strength in order to handle components
without damage after Injection Molding Process.
Typically, 55% by volume (18-wt. %) water is added to
the mixture, which performs the dual function of being a
solvent and a carrier for agar containing mixtures 3.
The mixture may also contain a variety of additives,
which can serve any number of useful purposes. For
example, dispersants may be employed to ensure a more
homogeneous mixture. Biocides may be used to inhibit
bacterial growth in the molding compositions, in
particular if they are to be stored for a long period of
time4.
The metal powder used is typically under 20 micrometers
and is made by gas or water atomization is shown in
Figure 1. The feedstock with a uniform composition of
high solid loading is desirable in the production of
Injection Molded parts. The higher solids loading
feedstock imparts lower shrinkage when the molded parts
are dried and fired, facilitating dimensional control
and reducing tendency for cracks during sintering
process, in turn higher yields of acceptable product
with lower scrap rates.
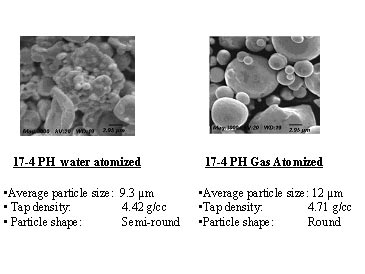
Figure 1. Water and Gas Atomized 17-4 PH Stainless Steel
Powders
The solid loading of the feedstock is near 92-wt % (61
vol. %), the balance consisting of water. The feedstock
is produced by passing mixture composition directly
through a twin screw extruder and cutting the extrudate
into pellets as it exits the die. Alternate method of
feedstock production is by mixing the mixture
composition in a sigma blender and then shredding the
blended mixture into pellets.
The feedstock is injection molded to the desired shape,
typically around 85o C melt temperature with a molding
pressure in the range of 150 psi to about 800 psi. At
injection molding temperature of 85o C the feedstock is
relatively fluid and is easily injection molded into a
net shape part. Compared to plastic injection molding,
water based agar system is molded at lower melt
temperature and injection pressure.
Once the feedstock temperature is cooled in the mold to
near room temperature, the green part can be ejected
from the mold. Typically injection molding cycle time is
in the order of 30 seconds depending on the part size.
The viscosity of the feedstock is similar to that of
unfilled Nylon 6 during injection molding process, as
shown in Figure 2. Due to the relative low molding
pressure and temperature required for water based agar
binder, soft tooling may be employed in place of
hardened tools for production runs less than 10,000
parts. 3D systems have developed SLA rapid tooling
fabricated directly from electronic files of a part. A
polymeric tool can be grown in a matter of hours at a
relatively low cost. Using water-based agar feedstock
prototype parts can be molded in a SLA tool.
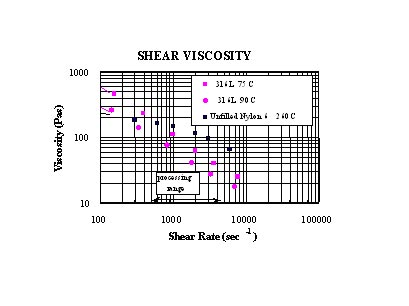
Figure 2. Aqueous Based Agar Binder 316L Stainless Steel
Viscosity Comparison with Unfilled Nylon 6 Polymer
The green part is left open in the ambient air for
approximately 1 hour for drying. No separate debind step
is required, as is necessary for traditional MIM
feedstock’s. For water based feedstock debind step is
incorporated into first one (1) hour cycle of the
sintering process. During the sintering process, the
binder pyrolizes in the sintering furnace and carbon is
removed during the sintering cycle. The sintering is
typically performed in Hydrogen medium for metal alloys
for carbon control, and air is typically used as a
medium for ceramics sintering. Sintering temperatures in
the range of 1300o – 1400o C are typically employed for
stainless steel alloys, and sintering temperatures in
the range of 1600o – 1700o C are typically employed for
Ceramic material such as Alumina. Batch or continuous
sintering furnaces can be employed for debinding/sintering
based on production volume requirements. The schematic
of ceramic and metal injection molding process using the
water based agar binder system is shown in Figure 3.
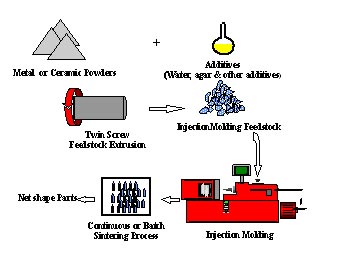
Figure 3. Schematics of Ceramic and Metal Injection
Molding Process using Water Based Agar Binder System
MICROSTRUCTURAL AND MECHANICAL PROPERTIES
The mechanical properties in 17-4PH Stainless Steel is
defined by uniform formation of martensite, which
requires control of carbon during sintering process. Due
to the low level of binder in water based agar
feedstock, as well as its relative ease in removal
during sintering process, carbon can be tightly
controlled. The typical specification of 17-4PH
stainless steel is below 0.07 wt % carbon. Carbon
Analysis in sintered components with a cross sectional
thickness of 19 millimeters manufactured from water
based agar system; carbon level is measured at .01% wt
%. The core and near surface of the component show a
uniform formation of martensite, demonstrating the tight
control of carbon achieved through the use of water
based agar feedstock system (5).
Many of the automotive applications require demanding
mechanical properties. Figure 4 lists the average
tensile properties of the 17-4PH stainless steel alloy6.
The samples consisted of two batches, UnHIPed and HIPed,
which were heat-treated to the H1025 condition. The 9.52
millimeter thick tensile bars employed in the study had
an average sintered density of 98.5 + 0.5%. The tensile
properties of water based agar system 17-4PH stainless
steel were equivalent to wrought and exceeded typical
cast properties. It was found that HIPed samples had
improved tensile properties due to 1-2% reduced porosity
compared to UnHIPed material (7).
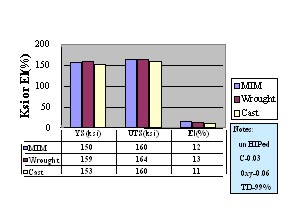
Figure 4. Average 17-4PH H1025 Stainless Steel Tensile
Data
DIMENSIONAL
CONTROL
Parts molded from water based agar system; there is an
approximate 2% shrinkage during drying and 17% shrinkage
during sintering process. This shrinkage is repeatable
resulting in control in dimensional tolerances to about
0.5% to a 3-sigma production yield. Tighter tolerances
can be obtained for critical dimensions through the use
of setters during the sintering process. Figure 5 shows
the current dimensional tolerance limits of Ceramic and
Metal Injection Molded Components (8).
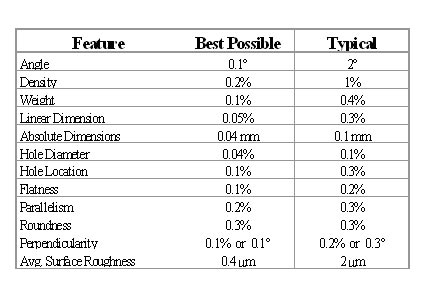
Figure 5. Current Dimensional Tolerance Limits for
Ceramics and Metal Injection Molded Components
AUTOMOTIVE APPLICATIONS
The water based agar binder system is available in a
variety of stainless steel alloys such as 17-4PH, 316L,
410 etc. as well as tungsten and nickel based super
alloys such as GMR 235, Hastelloy X etc. Additionally,
ceramics such as Alumina, Zirconia and Steatite can be
manufactured using water based Agar binder system.
Figure 6 shows a sintered automotive turbo charger wheel
made of the nickel alloy GMR2359. Figure 7 shows
balanced valve shaft for EGR system using 316L stainless
steel. Figure 8 shows automotive exhaust and electrical
components manufactured from Alumina and Steatite
Ceramics. Figure 9 shows advanced research concepts by
Mathson Industries on Exhaust Manifold technology using
metal, ceramic and metal or ceramic and plastic
Injection Molding solution.
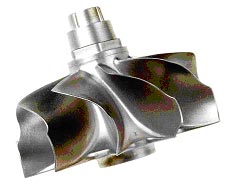
Figure 6. Sintered Automotive Turbocharger Wheels made
of the GMR235 Nickel Alloy
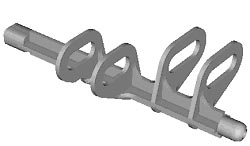
Figure 7. Balanced Valve Shaft for EGR System using 316L
Stainless Steel
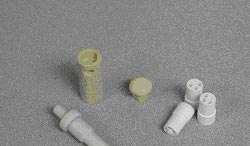
Figure 8. Automotive Exhaust and Electrical Components
Manufactured from Alumina and Steatite Ceramics
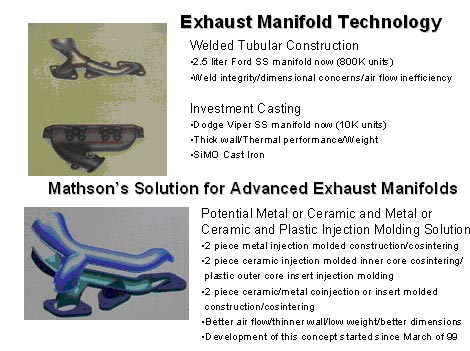
Figure 9. Advanced Exhaust Manifold Technology using
Metal or Ceramic and Metal or Ceramic and Plastic
Injection Molding Solution
CONCLUSION
Ceramic and Metal Injection Molding offers the ability
to produce large thick parts which are competitive with
those produced by Investment Casting. The mechanical
property of Injection Molded stainless steel alloy is
equivalent to wrought and exceeds typical cast
properties. Due to low molding pressure and temperature
required for Injection Molding, soft tooling could be
used for low production runs. Ceramics and metal alloys
Injection Molding can combine several machined or cast
components into one cost-effective product eliminating
several manufacturing steps.
Producing large parts such as exhaust manifolds in high
volumes can create a chain effect. For example the
automotive exhaust manifold annual usage in North
America exceeds more than 17 million units and each
manifold weighs several pounds, the total annual usage
of the material will be several million pounds. This
will allow raw material suppliers to produce powders at
a reasonable cost. The feedstock price will decrease, as
the powder price is the largest cost component of the
feedstock. This will then increase the potential for
part suppliers to produce parts at a competitive price.
This will enable PIM technology to produce other
applications, which currently cannot be produced due to
prohibitive feedstock cost.
ACKNOWLEDGEMENTS
The author would like to thank Cathy Mathew and Jane
Salvati of Mathson Industries, Inc. for their valuable
suggestions and assistance with this project.
AUTHOR’S BIOGRAPHY
Boney A. Mathew is President & CEO of Mathson
Industries, Inc., Mathson Materials Technology, Inc. and
Mathson Intellectual Technology, Inc., Troy, Michigan,
USA. Mathson Industries is a leading supplier of
Ceramics, Metal Alloys, Elastomers, and Plastics
Injection Molded Systems and Assemblies, globally.
Mathson Materials Technology is a leading materials
supplier of Ceramics and Metal Alloys for the Powder
Injection Molding Industry. Mathson Intellectual
Technology provides Patented New Products and
Technology, globally.
Mr. Mathew’s background includes eighteen years in the
automotive and plastics industry.
Prior to starting Mathson Industries, Inc., he was a
Marketing and Technical Executive for Nyltech North
America - Joint Venture of Rhone-Poulenc - France and
Fiat - Italy.
He also served as Plastics Manager for Teleflex, Inc.’s
Automotive, Aerospace and Medical Company. Mr. Mathew is
the inventor and co-inventor of several patents,
including “Method of Making Fluorocarbon Coated
Composite Braided Hose Assemblies”, “Hose End Fitting
Assembly” and “Expanded Fluoropolymer Tubular Structure,
Hose Assembly and Method for Making Same”.
He is a member of the Society of Plastics Engineers,
Society of Automotive Engineers, APMI and ASEI. He has
published and presented twelve technical publications on
various plastics, ceramics, metals and composites at
various international technical conferences and is the
co-author of “Passage to India, A Comprehensive Study on
the Indian Automotive Industry”.
Mr. Mathew earned Bachelor of Science and Master of
Science degrees in Plastics Engineering from the
University of Massachusetts, Lowell, Massachusetts USA.
REFERENCES
1. German, R., & Bose, A., “Injection Molding of Metals
& Ceramics”, Metal Powder Industries Federation, 1997,
pp. 209-210.
2. Fenelli et al., “Gel Strength enhancing additives for
agaroid-based Injection Molding Compositions”, United
States Patent Number 5,746,957, May 5, 1998, p.4.
3. ibid., p. 6
4. ibid., p. 6
5. Lasalle, J., “Net Shape Processing of Metals Using
and Aqueous – Based Injection Molding Binder”.
6. ibid., p. 3
7. ibid., p. 4
8. German, R., opcit. p. 288.
9. Lasalle, J., opcit., p. 5.
|