Automotive Air Intake Manifold Application using Nylon
6,6 Composite Material
SAE
TECHNICAL PAPER SERIES 1999-01-3011 E
Boney A. Mathew
Mathson Industries, Inc.
Dr.
Helio Wiebeck
Engenharia Quimica
University of Sao Paulo
Copyright © 1999 Society of Automotive Engineers, Inc.
ABSTRACT
There are many
advantages to air intake manifolds molded from Nylon 6.6
Glass reinforced composite material versus a
pressure-cast aluminum manifold. Weight is significantly
lowered and production costs generally are reduced.
Performance improves with the precise control of the
interior surface finish and reduced air induction
temperatures. The Nylon 6,6 Glass reinforced composite
material can be molded into intricate shapes by
injection molding or lost-core process with reduced
machining operations as well as Nylon 6,6 material is
easily recycled. Production costs will continue to
decrease as optimization of material, process and part
integration increases.
This study
evaluates Nylon 6,6 Glass reinforced composite material
in terms of the intake manifolds material key
requirements such as thermal, heat aging, fatigue,
impact, creep, stress and chemical resistance including
multi fuels. This study would assist engineers in
designing intake manifolds using Nylon 6,6 Glass
reinforced composite material.
INTRODUCTION
For over 25
years Nylon 6,6 Glass reinforced composite material has
been used in under the hood applications. Some of the
under the hood applications using Glass reinforced Nylon
6,6 are brake and power steering fluid reservoirs,
radiator end tanks, fuel injectors, etc. In recent years
Glass reinforced Nylon 6,6 composite has been used for
injection molded and loss core molded air intake
manifold.
The Nylon 6,6
composite offers several economic benefits. An air
intake manifold made from Nylon 6,6 composite can be
molded with snap-on or clip-on features due to the
strength and flexibility of the material. This
significantly reduces assembly costs as much as 15 –
20%. The Nylon 6,6 composite manifold requires no paint,
is non-corrosive and non-porous, unlike cast aluminum
which requires costly finishing steps.
The improved
volumetric efficiency of an intake manifold made from
Nylon 6,6 composite is due to its inherent insulating
properties. The Nylon 6,6 composite can be designed and
molded with greater flexibility than cast aluminum. The
manifold can be produced with a smoother, streamlined
interior, resulting in increased airflow to the engine,
which is a key factor in increasing horsepower of the
engine.
An air intake
manifold molded from Nylon 6,6 composite is an important
factor when faced with the proposed stricter corporate
average fuel economy (CAFÉ) regulations.
In short, Nylon
6,6 Glass reinforced composite offers several
advantages. It saves money, reduces weight, ease of
assembly, better insulation, improved airflow, excellent
strength to weight ratio and is recyclable.
EXPERIMENTAL
In order to
study the effect the automotive environment has on the
long term mechanical durability of Nylon 6,6 Glass
reinforced composite for air intake manifolds, the
following methodology was established:
-
Characterize the material by performing physical
properties tests.
- Expose the
material to various temperatures to evaluate thermal
resistance of the material in order to simulate
conditions under the hood.
- Expose the
material to fuels to evaluate chemical resistance of
the material.
MATERIAL
SSD 330 KNF, 33%
Glass reinforced polyamide 6,6 provided by Nyltech North
America.
EQUIPMENT
A 70mm ZSK 70
Werner and Pfleiderer twin screw extruder was employed
for compounding the material.
PHYSICAL
PROPERTIES TEST
Test specimens
were molded and tested using SSD 330 KNF material to
obtain physical properties of the material. The test
specimens were exposed to various temperatures and fuels
to understand the long term properties which would
assist in qualifying this material for intake manifold
applications.
RESULTS AND
DISCUSSION
This study was
conducted to characterize and to qualify Nylon 6,6 Glass
reinforced composite for intake manifold applications.
Table I shows
the physical properties data for Nylon 6,6 – 33% Glass
reinforced composite material. Table II shows stress
versus strain data at –40º to 150ºC for Nylon 6,6 – 33%
Glass reinforced composite. As expected at -40ºC at
given strain stress is maximum and at 150ºC stress is
minimum. This is due to viscoelastic relaxation's
corresponding to the onset of various types of internal
motion with increasing temperature (1).
Figure 1
graphically shows tensile creep of the Nylon 6,6 – 33%
Glass reinforced composite. A percentage creep at 70ºC
is higher than at 20ºC. At higher temperatures, the
atoms and groups in the polymer molecules acquire an
increasing amount of thermal energy, causing them to
vibrate and move about. The higher the temperature, the
greater the thermal motion. The larger the sequences of
atoms in the polymer chain which become mobile, and in
turn increase creep at higher temperature (2).
Figure 2, 3 and
4 shows the effects of heat aging at 150ºC on tensile
strength, ultimate elongation, and Young's modulus for
Nylon 6,6 – 33% Glass reinforced composite. After 2000
hours at 150ºC Nylon 6,6 – 33% Glass reinforced
composite showed good thermal durability based on
retention of the properties. The properties after 500 to
1000 hours remained fairly constant or increased
slightly. This indicated that while chain scission is
occurring on the surface due to oxidation, chain linking
(solid-state polymerization) occurs internally,
resulting in a constant or higher stiffness.
Additionally, it is attributed to stress relieving and
further crystallization at 150ºC.
The reduction in
properties at 2000 hours at 150ºC is primarily caused by
free radical chain scission and cross-linking of the
polymer molecules close to the surface. Three primary
mechanisms that change the mechanical properties of a
polymer exposed to higher temperatures are chain
scission, cross-linking and oxidation. In most cases,
all three mechanisms occur simultaneously. Their effects
may balance each other for a while, but eventually one
of the reactions prevails, leading to embrittlement of
the polymer (4).
Figure 5 shows
the effects of M-20 fuel soak at 121ºC for 500 hours on
tensile strength for Nylon 6,6 – 33% Glass reinforced
composite. The tensile strength dropped significantly
after 500 hours at 121ºC when soaked in M-20 fuel. Nylon
6,6 is known to be adversely affected by exposure to
methanol. Methanol is absorbed by nylon and thus causes
reversible mechanical property changes due to
plasticization. Methanol will also hydrolyze nylon at
higher temperatures. Dried out samples after exposure to
M-20 fuel regained most of the original tensile strength
due to evaporation of absorbed fuel.
Figure 6, 7 and
8 shows Peugeot, Fiat and Alfa Romeo air intake
manifolds using Nylon 6,6 Glass reinforced composite
material.
CONCLUSIONS
Within the limit
of this study, it is shown that Nylon 6,6 – 33% Glass
reinforced composite material is suitable for intake
manifold applications. This material has high strength
and toughness, and excellent retention of properties
after heat aging.
REFERENCE
(1) Kohen
M.I., Nylon Plastics, John Wiley & Sons Inc., N.Y. 1973,
P. 313
(2)
Deanin R.D., Polymer Structure, Properties and
Applications, Cahner Publishing Co.,
N.Y., 1972, P. 88
(3) Murty
E.M., The Effect of the Automotive Fuel System
Environment on the Long
Term Durability of Reinforced Nylon, Thesis to GMI
Engineering and Management
Institute, April 15, 1989, P. 28
(4) Ibid,
P. 29
AUTHOR'S
BIOGRAPHY
Mr. Boney
Mathew, President & CEO, Mathson Industries, Inc., Troy,
Michigan USA.
Mr. Mathew's
background includes 16 years in the automotive and
plastics industry.
Prior to
starting Mathson Industries, Inc., he was a Marketing
and Technical Executive for Nyltech North America –
Joint Venture of Rhone-Poulenc – France and Fiat –
Italy.
He also served
as Plastics Manager for Teleflex, Inc.'s Automotive,
Aerospace and Medical Company. Mr. Mathew is the
inventor and co-inventor of several patents including
"Method of Making Fluorocarbon Coated Composite Braided
Hose Assemblies", "Hose End Fitting Assembly" and
"Expanded Fluoropolymer Tubular Structure, Hose Assembly
and Method for Making Same".
He is a member
of Society of Plastics Engineers, Society of Automotive
Engineers and ASEI. He has published and presented six
technical publications on various plastics and
composites at various international technical
conferences and is the co-author of "Passage to India, A
Comprehensive Study on the Indian Automotive Industry."
Mr. Mathew
earned a M.S. degree in Plastics Engineering from the
University of Massachusetts, Lowell, USA.
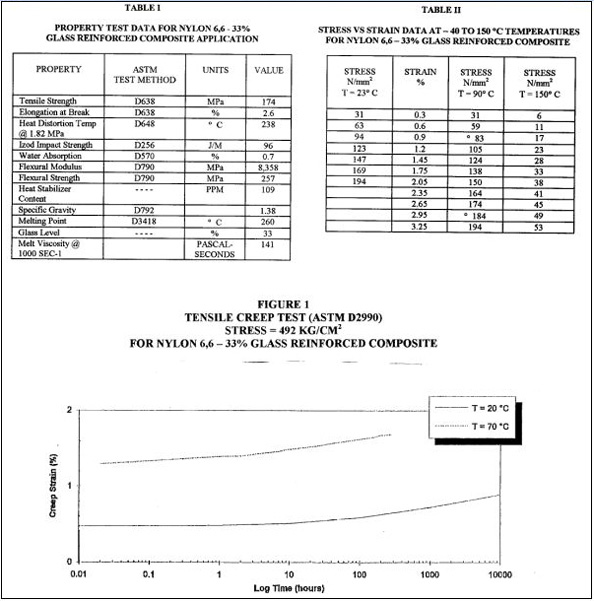
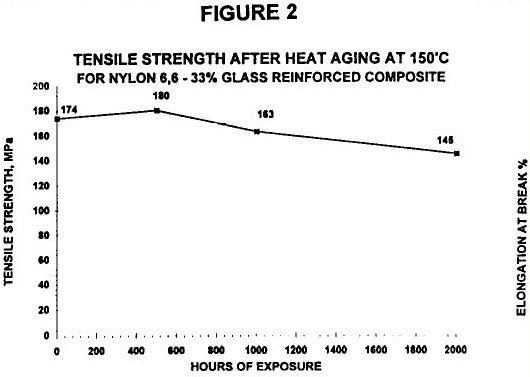
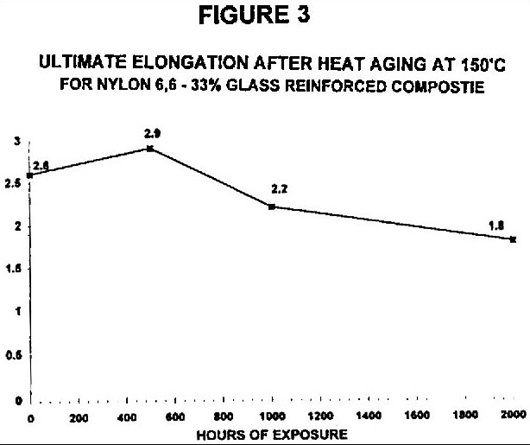
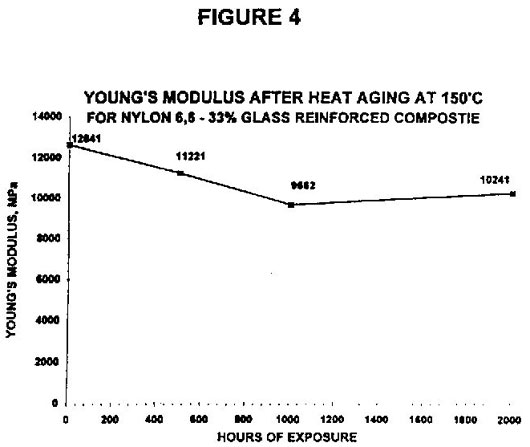
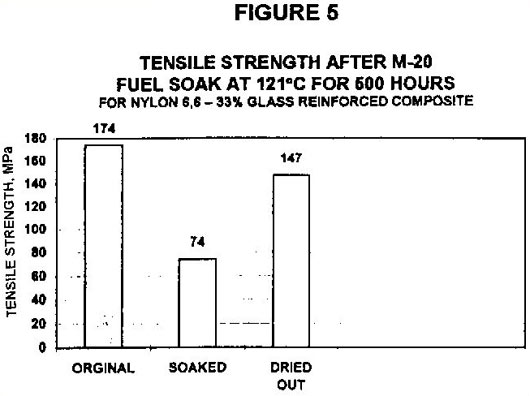
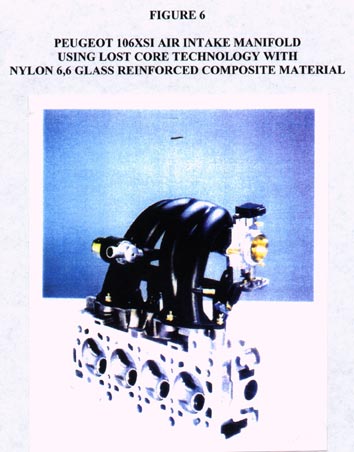
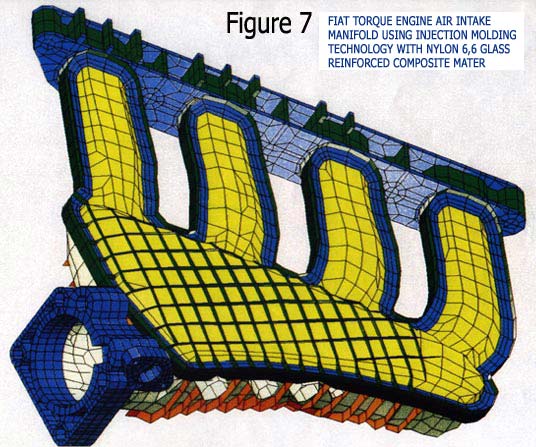
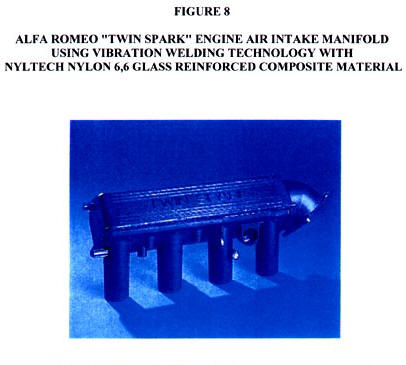
The appearance of
the ISSN code at the bottom of this page indicates SAE’s
consent that copies of the paper may be made for
personal or internal use of specific clients. This
consent is given on the condition however, that the
copier pay a $7.00 per article copy fee through the
Copyright Clearance Center, Inc. Operations Center, 222
Rosewood Drive, Danvers, MA 019223 for copying beyond
that permitted by Sections 107 or 108 of U.S. Copyright
Law. This consent does not extend to other kinds of
copying such as copying for general distribution, for
advertising or promotional purposes, for creating new
collective works, or for resale.
SAE routinely
stocks printed papers for a period of three years
following date of publication. Direct your orders to SAE
Customer Sales and Satisfaction Department.
Quantity reprint
rates can be obtained from the Customer Sales and
Satisfaction Department.
To request
permission to reprint a technical paper or permission to
use copyrighted SAE publications in other works, contact
the SAE Publications Group.
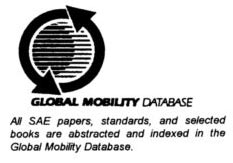
No part of this
publication may be reproduced in any form, in an
electronic retrieval system or otherwise, without the
prior written permission of the publisher.
ISSN 0148-7191
© Copyright 1999 Society of Automotive Engineers, Inc.
Positions and
opinions advanced in this paper are those of the
author(s) and not necessarily those of SAE. The author
is solely responsible for the content of the paper. A
process is available by which discussions will be
printed with the paper if it is published in SAE
Transactions. For permission to publish this paper in
full or in part, contact the SAE Publications Group.
|